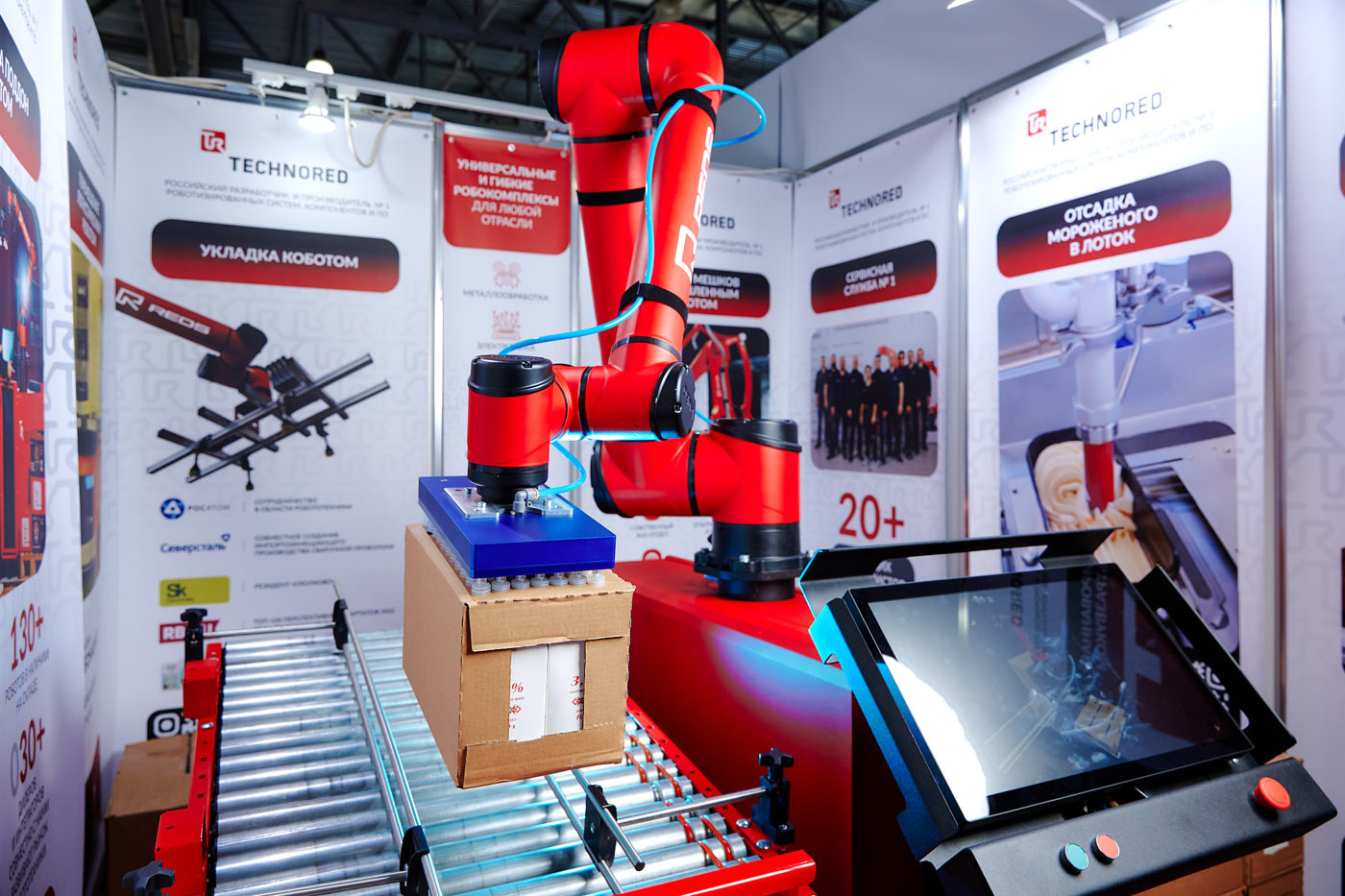
По данным Роспотребнадзора, в топ самых опасных для здоровья сфер деятельности входят предприятия транспортировки и хранения. Уровень профессиональной заболеваемости в этих областях составляет 10,56%, уступая печальную участь лидера лишь добывающей отрасли.
На производствах процессы, связанные с перемещением грузов, тоже входят в число проблемных как с точки зрения безопасности труда, так и с точки зрения эффективности. Например, низкая производительность, порча готовой продукции, нехватка кадров — типичные проблемы процессов упаковки и перемещения готовой продукции на склад или в зону отгрузки. Именно поэтому эти физически тяжелые, травмоопасные рутинные процессы входят в топ самых желанных для автоматизации и роботизации.
Чем поможет робот
Для хранения и транспортировки готовой продукции современные производства применяют паллетирование. Это универсальная упаковка максимально компактным способом с использованием специального плоского поддона (паллеты). Паллетирование — оптимальный вариант, когда товар состоит из небольших коробок с хрупкими и тяжелыми предметами. Подробно разберем автоматизацию процесса на примере паллетирования.
Роботы имеют ряд преимуществ перед традиционными методами паллетирования. Роботы более точны и аккуратны, чем люди, что снижает вероятность ошибок и повреждений грузов.
Важно, что роботы могут работать в опасных или вредных для человека условиях. Головная боль инженера по охране труда — пыль, шум, микроклимат, световая среда — не являются проблемой для робота.
К опасным производственным факторам относятся тяжесть труда и его напряженность. Руководство по гигиене труда предписывает мужчине поднимать не более 30 кг не чаще двух раз в час. Груз весом 50 кг поднимать можно, но только вдвоем. Остальные режимы работы наносят ущерб здоровью.
Решить проблему производительности, не рискуя нарушить этические и юридические нормы, можно с помощью автоматизации. Роботы способны работать в режиме 24\7, что позволяет кратно повысить эффективность процессов на предприятии.
Разберем нюансы автоматизации
Важно понимать, что автоматизация — это комплексный процесс, и его нужно грамотно организовать. Роботы — ключевое, но не единственное звено промышленной автоматизации. Что еще необходимо сделать для автоматизации:
1. Организовать подачу продукции к месту паллетирования (укладки). Это задача конвейера.
2. Обеспечить повторяемость положения в точке захвата. Проще говоря, то, что роботу нужно захватить своей сильной рукой, должно каждый раз быть на одном и том же месте в одном и том же положении. Для решения этой задачи проще всего установить на конвейер направляющие и ограничители.
3. Чтобы робот понимал, что продукт достиг точки захвата, нужно оснастить конвейер датчиком наличия продукции. Датчик устанавливается на конвейер и подключается к роботу.
4. Организовать место укладки. Паллеты должны быть каждый раз на одном и том же месте в одном и том же положении. Повторяемость установки паллет надежнее всего организовать за счет ограничителей, на которые стоит установить датчики наличия паллет.
5. Организовать своевременную смену заполненных паллет. Для этого необходимо создать индикацию для операторов. Следующим этапом автоматизации может стать организация мобильной платформы, которая забирает паллеты на склад или в место погрузки.
6. Внимание на безопасность! Современные роботы безопасны, но пренебрегать правилами работы с ними нельзя.
А теперь реальный пример.
Дано: мешки со строительной смесью весом от 15 до 40 кг на заводе Прикамской гипсовой компании.
Задача: автоматизировать укладку мешков на поддоны с производственной линии в условиях ограниченного пространства.
Решение: автоматизировать выдачу поддонов, укладку поддонов в место паллетирования, транспортирование заполненной паллеты в зону выгрузки. Для этого потребуется четырехосевой промышленный робот TECHNORED с универсальным клещевым захватом мешков, диспенсер поддонов, конвейерная линия транспортирования с датчиками пустых поддонов и заполненных паллет.
Как это работает: робот-паллетайзер укладывает поддоны в зону загрузки, мешки на поддон в соответствии с выбранным рецептом. После заполнения паллет по конвейерной системе продукция передается из зоны укладки в безопасную зону выгрузки.
Результат: производительность взлетела до 750 мешков в час.
Общая площадь, занятая роботизированным комплексом — 35 кв. метров.
Здоровье сотрудников предприятия неоценимо.